
28
2022
/
04
28
2022
/
04
28
2022
/
04
Website
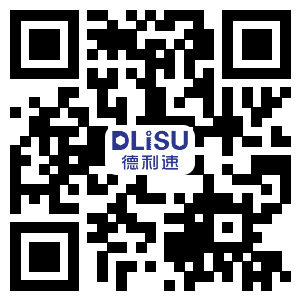
Shenzhen Dlisu Printing Machinery Co., Ltd.
Shenzhen Address: 803, Shenbao Building, No. 219, Zhenming Road, Gongming Street, Guangming New District, Shenzhen
Shantou Address: Wanji Industrial Zone (Second Branch Road), Longhu District, Shantou City
Tel: 86-754-87224116
Phone: 86-137-5047-4043
86-138-2327-5809 86-159-1664-0313
Fax: 86-754-87224116
QQ: 815887412
E-Mail:dlisu888@163.com