
Application of Heidelberg Online Glazing System
Time:
2021-09-15
Nowadays, the surface treatment of printed matter is not only limited to hot stamping, gluing, embossing and other processes, but also chooses glazing process to improve the brightness and feel of printed matter. Glazing has been regarded as a very potential surface finishing process by printing enterprises. Major printing machinery and equipment manufacturers have also invested a lot of manpower and material resources to develop a variety of glazing equipment. Because online glazing is much more economical and better in quality than single glazing after printing, online glazing technology has been widely used and developed. Next, the author introduces and analyzes the online glazing system of Heidelberg Speed Blaster CD102-7+LY+UV+CP2000.
Varnish
The online glazing system of CD102-7+LY+UV+CP2000 can be used for water-based glazing and UV glazing. Generally speaking, the cost of online glazing is equivalent to printing another color of ink.
Because the coating of water-based varnish is slightly thicker than that of UV varnish, the amount of water-based varnish consumed by the same print is more. Waterborne varnish can not only increase the glossiness of printed products, but also has the characteristics of fast drying speed, stable coating, good friction resistance and no odor. In addition, there is no need to spray powder or only a small amount of powder in the water-based glazing process, which also brings great convenience to post press processing, is conducive to the close connection of various processes, and is also conducive to ensuring the delivery date of printed products. Waterborne varnish is the most environmentally friendly varnish at present. It is non-toxic, convenient and quick to clean, and will not damage the health of operators. It is widely used.
There are nearly 60% water, about 40% lotion resin, 1% ~ 3% emulsifier and 2% ~ 5% IPA (isopropyl alcohol) in the aqueous varnish. The viscosity of the varnish should be controlled within 35 ~ 40s. If the viscosity of varnish is large, when coating paper with a fixed weight of 128g/m2 or less, the paper will absorb some water during coating and curl. At this time, the force between the paper and the blanket may be greater than the tension between the teeth of the embossing cylinder and the paper. The paper is easy to stick to the blanket, causing difficulties in operation.
UV varnish is more suitable for online coating, which has the following advantages: ① Good coating effect, high gloss printing. ② The coating has good friction resistance. ③ The curing speed is fast, the production process does not need powder spraying, and there is no adhesion between prints, which improves the production efficiency. However, UV varnish also has the following disadvantages: ① The price of UV varnish is higher than water-based varnish, and the coating equipment is also more expensive. ② UV varnish has certain toxicity, and it is easy to harm human skin after long-term contact. ③ After the traditional printing is completed, the printed matter needs to be completely dried before the UV varnish can be applied online. ④ Printing needs to be stored for a period of time after glazing to slowly eliminate the smell of UV varnish.
Glazing device
The glazing device of CD102-7+LY+UV+CP2000 is generally divided into two types: box scraper glazing system and double roller glazing system. Customers can choose any one according to their own requirements.
As the name implies, the box type scraper polishing system is equipped with two scrapers in the box. The position of the scrapers is opposite from top to bottom, which is very sharp, and can better ensure the stability of the polishing. Its price is more expensive than the double roll polishing system. When applying the box type scraper polishing system, special attention should be paid to: when the polishing is not required, the scraper must be separated from the anilox roller to avoid damage.
The double roll glazing system changes the amount of glazing by increasing the pressure between the liquid bucket roll and the glazing roller. When the running speed of the printing machine is increased, the speed of the bucket roller can be increased through the CP2000 control system, but the oil is easy to overflow when there is time. When the double roll glazing system is not used, pay attention to the clutch of the bucket roll to avoid damage to the rubber roll caused by dry friction.
No matter which glazing system is used, the following problems should be noted. ① When installing the blanket, be sure to drop the safety roll, press the blanket, and then slowly order the vehicle. This is because the rubber roller and the backing roller operate in the opposite direction, and the backing roller is relatively fast. It is necessary to prevent the blanket from being drawn into the scraper system with the glazing rubber roller, causing damage to the scraper and the blanket. ② In the overall glazing, the size of the blanket should be as small as possible than the size of the original paper, but it should be controlled outside the bleeding position of the paper, which can reduce the waste of varnish. ③ The shutdown shall be avoided as far as possible. After the shutdown, the blanket must be cleaned to keep it clean. ④ For regular geometric figures, the design department can first put together a piece of film, expose and print the non glazing area of the film, print with white ink, and then carve and dig the blanket to remove the adhesive layer of the parts that do not need glazing, and then clean the blanket to conduct local glazing. As the blanket is carved, the edge of the carved part will be eroded by varnish, causing the edge of the print to fuzz. We can also consider using a photosensitive resin plate to replace the blanket, but the photosensitive resin plate should have the following conditions: the thickness of the plate is uniform, the light oil can be transferred evenly, the performance is stable under high-speed operation for a long time, and the accumulation of light oil should be small, at the same time, it needs to find a professional plate making company to make it.
Website
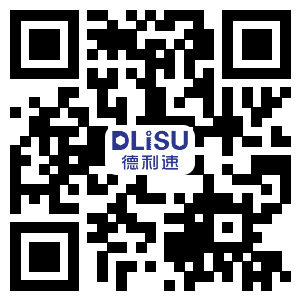
Shenzhen Dlisu Printing Machinery Co., Ltd.
Shenzhen Address: 803, Shenbao Building, No. 219, Zhenming Road, Gongming Street, Guangming New District, Shenzhen
Shantou Address: Wanji Industrial Zone (Second Branch Road), Longhu District, Shantou City
Tel: 86-754-87224116
Phone: 86-137-5047-4043
86-138-2327-5809 86-159-1664-0313
Fax: 86-754-87224116
QQ: 815887412
E-Mail:dlisu888@163.com